X60/X70 high-grade spiral welded pipes - low-temperature impact resistance, preferred for polar oil and gas pipelines
Category:
Summary description:
Keywords:
Details
In the extreme and unforgiving environments of the polar regions, where temperatures plummet to -50°C and beyond, the infrastructure supporting oil and gas exploration and transportation faces challenges unlike any other. Among the critical components enabling safe and reliable operations in these harsh conditions are X60/X70 high-grade spiral welded pipes, engineered to deliver exceptional strength, durability, and, most importantly, low-temperature impact resistance. These pipes have become the preferred choice for polar oil and gas pipelines, combining advanced metallurgy, precision manufacturing, and a design tailored to withstand the unique stresses of extreme cold, making them indispensable in unlocking the energy resources of the world’s frozen frontiers.
At the core of X60/X70 pipes’ performance is their high-grade steel composition, a result of meticulous alloy design and heat treatment processes. The “X” in their designation refers to their classification under API 5L, the global standard for line pipe used in oil and gas transportation, with the numbers indicating their minimum yield strength in megapascals (X60: 414 MPa; X70: 483 MPa). These high yield strengths mean the pipes can withstand the high internal pressures of oil and gas transmission—often exceeding 10 MPa—while maintaining their structural integrity. What sets X60 and X70 apart, particularly in polar applications, is their optimized chemical composition: low carbon content to enhance weldability, controlled levels of manganese and niobium to improve strength, and the addition of microalloying elements like vanadium or titanium to refine grain structure. This grain refinement is critical for low-temperature performance, as smaller, more uniform grains prevent the brittle fracture that can occur in larger-grained steels when exposed to extreme cold.
The low-temperature impact resistance of X60/X70 spiral welded pipes is their defining attribute, a feature that makes them uniquely suited for polar environments. In sub-zero temperatures, most metals become increasingly brittle, with a sharp drop in their ability to absorb energy before fracturing—a phenomenon known as the ductile-to-brittle transition. X60/X70 steels are engineered to shift this transition temperature well below the extreme lows of polar regions, ensuring they remain ductile even at -50°C. This is verified through rigorous Charpy V-notch impact testing, where samples are cooled to polar temperatures and struck with a pendulum; X60/X70 pipes consistently absorb sufficient energy (typically 40 J or more) to avoid brittle failure. For polar pipelines, this resistance is non-negotiable: a single fracture in a pipeline carrying high-pressure oil or gas could lead to catastrophic leaks, environmental contamination, and the loss of valuable resources. The ability to withstand sudden impacts—from ice movement, ground shifts, or equipment collisions—without fracturing ensures the pipeline remains operational even in the most unpredictable polar conditions.
The spiral welded design of these pipes complements their high-grade steel properties, offering structural advantages that enhance their suitability for polar oil and gas pipelines. Spiral welding involves forming a continuous steel strip into a helical shape and fusion-welding the overlapping edges, creating a pipe with a strong, uniform seam that runs at an angle to the pipe’s axis. This spiral seam distributes stress evenly around the pipe’s circumference, making it highly resistant to the internal pressure of the conveyed fluids and the external stress of frozen ground. Unlike straight-seam pipes, which may have weaker points along their longitudinal joints, spiral welded pipes exhibit consistent strength throughout their length, reducing the risk of failure in areas where the pipeline bends or is exposed to uneven ice loads. The spiral design also allows for the production of long, continuous pipe lengths (up to 12 meters or more), minimizing the number of field joints—critical in polar regions where welding in extreme cold is challenging and prone to defects. Fewer joints mean fewer potential leak points, simplifying maintenance and enhancing the pipeline’s overall reliability.
X60/X70 spiral welded pipes are preferred for polar oil and gas pipelines not only for their low-temperature performance but also for their ability to address the unique logistical and environmental challenges of these regions. Polar oil and gas fields are often remote, with limited infrastructure and extreme weather conditions that make transportation and installation difficult. The high strength-to-weight ratio of X60/X70 steels allows for lighter pipes that are easier to transport by ice roads, ships, or aircraft, reducing logistical costs and complexity. Their spiral design also enables flexibility, allowing the pipeline to adapt to minor ground movements caused by permafrost thawing and freezing—a common issue in polar regions where temperature fluctuations can shift the soil. This flexibility prevents the pipeline from developing excessive stress that could lead to cracks or weld failures. Additionally, the pipes can be coated with specialized anti-corrosion layers, such as three-layer polyethylene (3LPE) or fusion-bonded epoxy (FBE), to resist the corrosive effects of saltwater (in offshore polar projects) and the harsh chemicals present in some oil and gas mixtures, ensuring long-term performance in environments where maintenance is costly and infrequent.
In polar applications, operational efficiency is as critical as structural integrity, and X60/X70 spiral welded pipes deliver on this front as well. The smooth internal surface of these pipes, a result of precision manufacturing, minimizes friction, allowing oil and gas to flow with greater efficiency and reducing the energy required for pumping. This is particularly important in polar regions, where energy sources are limited and expensive. The high flow capacity of X60/X70 pipes, enabled by their large diameters (up to 1422mm), also supports the high production rates needed to justify the investment in polar oil and gas projects. For subsea polar pipelines, which must withstand extreme hydrostatic pressure and ice scouring, the combination of high-grade steel and spiral welding ensures the pipes can operate at depths of hundreds of meters without collapsing or deforming. Their resistance to fatigue—caused by repeated pressure cycles from oil and gas flow—also ensures a long service life, often exceeding 30 years, which is essential for recouping the significant capital investment in polar infrastructure.
Environmental sustainability is an increasingly important consideration in polar oil and gas development, and X60/X70 spiral welded pipes contribute to responsible operations in several ways. Their long service life reduces the need for frequent pipeline replacements, minimizing the environmental footprint of construction activities in fragile polar ecosystems. The high-strength steel used in their production is 100% recyclable, aligning with global efforts to reduce waste and promote circular economies. Additionally, their leak-resistant design and corrosion protection help prevent oil and gas spills, which could have devastating effects on polar wildlife and ecosystems. For operators seeking to minimize their environmental impact, X60/X70 pipes offer a balance between performance and sustainability, ensuring that energy extraction in polar regions is done with the least possible harm to the environment.
The versatility of X60/X70 grades allows engineers to select the optimal pipe for specific polar project requirements. X60, with its lower yield strength compared to X70, is often chosen for onshore polar pipelines where pressure requirements are moderate and cost efficiency is a priority. X70, with its higher strength, is preferred for high-pressure offshore pipelines or projects where the pipeline must withstand extreme ice loads or deepwater pressures. Both grades can be customized with varying wall thicknesses (from 8mm to 30mm) to meet specific design criteria, ensuring that the pipe’s strength matches the project’s needs without unnecessary weight or cost. This flexibility makes X60/X70 spiral welded pipes suitable for a range of polar applications, from gathering lines in ice-covered fields to long-distance transmission pipelines connecting remote fields to processing facilities.
In conclusion, X60/X70 high-grade spiral welded pipes represent the pinnacle of engineering for polar oil and gas pipelines, combining high strength, low-temperature impact resistance, and a durable spiral design to meet the demands of extreme cold environments. Their ability to withstand -50°C temperatures without brittle failure, combined with their resistance to pressure, corrosion, and environmental stress, makes them the preferred choice for unlocking the energy resources of the polar regions. Whether used in onshore permafrost or offshore ice-infested waters, these pipes deliver the reliability, efficiency, and sustainability needed to operate safely and responsibly in the world’s harshest conditions. As polar oil and gas exploration continues to expand, X60/X70 spiral welded pipes will remain a critical technology, enabling the development of these resources while protecting both workers and the fragile polar ecosystem.
More Products
Message
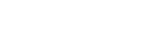
All Rights Reserved Copyright © RIZHAO STEEL HOLDING GROUP CO.,LTD. SEO 【Business license】
All Rights Reserved Copyright © RIZHAO STEEL HOLDING GROUP CO.,LTD.