3PE anti-corrosion reinforced spiral steel pipes - anti-corrosion for underground pipe networks, with attached inspection reports
Category:
Summary description:
Keywords:
Details
In the hidden world of underground infrastructure, where pipes are subjected to relentless attacks from soil chemicals, moisture, and physical stress, the choice of materials directly impacts the longevity and reliability of critical systems. 3PE anti-corrosion reinforced spiral steel pipes have emerged as a gold standard in this challenging environment, offering unmatched protection against corrosion while delivering the structural strength needed for underground pipe networks. Combined with comprehensive inspection reports, these pipes provide a level of assurance that is indispensable for engineers, contractors, and municipalities tasked with building infrastructure that stands the test of time.
At the core of these pipes’ exceptional performance is the 3PE anti-corrosion coating, a multi-layered system engineered to create an impenetrable barrier against corrosion. The term “3PE” refers to the three layers that compose the coating: a fusion-bonded epoxy (FBE) primer, an adhesive layer, and a polyethylene (PE) topcoat. Each layer plays a critical role in protecting the steel substrate. The FBE primer, applied directly to the pre-treated steel surface, forms a strong chemical bond with the metal, providing excellent adhesion and resistance to cathodic disbondment—a common failure mode in corrosion protection systems. The middle adhesive layer ensures a secure bond between the FBE primer and the outer PE layer, preventing delamination even under extreme temperature fluctuations or soil movement. The outer PE layer, a tough and flexible polymer, acts as the first line of defense against physical damage, moisture, and chemical attack from soil contaminants such as sulfates, chlorides, and acids. Together, these three layers create a synergistic protective system that outperforms single-layer or dual-layer coatings, extending the service life of underground pipes by decades compared to unprotected or traditionally coated steel.
The reinforced spiral steel structure of these pipes complements the 3PE coating, providing the mechanical strength required to withstand the rigors of underground installation and operation. Spiral steel pipes are manufactured by rolling a continuous steel strip into a helical shape and welding the edges, creating a structure with inherent strength and uniformity. The spiral weld distributes stress evenly around the pipe’s circumference, making it highly resistant to external pressure from soil loads, traffic vibrations, and ground settlement—common challenges in underground networks. The reinforced design, which often includes thicker walls or higher-grade steel alloys, enhances this resistance, allowing the pipes to maintain their integrity even in compacted soils or areas with high groundwater pressure. This structural robustness is particularly critical for underground applications such as water mains, gas pipelines, and sewage systems, where pipe failure can lead to costly leaks, service disruptions, and environmental contamination. Unlike rigid pipes that may crack under stress, the spiral design offers a degree of flexibility, enabling the pipes to adapt to minor ground movements without compromising the 3PE coating or the steel substrate.
For underground pipe networks, where corrosion is the primary enemy, 3PE anti-corrosion reinforced spiral steel pipes deliver unparalleled protection. Underground environments are inherently hostile to steel: soil moisture creates an electrolytic medium for corrosion, while bacteria in anaerobic conditions produce hydrogen sulfide, a highly corrosive gas. Traditional steel pipes, even those with basic coatings, often succumb to these forces within 10–15 years, requiring expensive replacements. In contrast, the 3PE coating system is specifically engineered to resist these threats. The FBE layer prevents the diffusion of water and ions to the steel surface, while the PE layer blocks the entry of corrosive chemicals and physical abrasion from soil particles. This protection is so effective that 3PE coated pipes are specified in some of the most demanding underground applications, including cross-country oil and gas pipelines, municipal water distribution systems, and industrial wastewater networks. In coastal areas, where saltwater intrusion is a risk, or in industrial zones with contaminated soil, the 3PE coating provides an extra layer of security, ensuring that the pipes remain functional even in highly aggressive environments.
A key feature that sets these pipes apart is the attached inspection reports, which provide verifiable proof of quality and performance. These reports are generated through rigorous testing conducted during and after production, covering every aspect of the pipe’s construction and coating. Tests include adhesion strength measurements to ensure the 3PE coating bonds properly to the steel, impact resistance tests to verify the coating’s ability to withstand installation damage, and cathodic disbondment tests to assess long-term adhesion under electrochemical stress. The reports also document the results of mechanical tests on the steel substrate, such as tensile strength and weld quality inspections, ensuring the pipe meets or exceeds industry standards for structural performance. For project stakeholders, these inspection reports serve as a critical tool for quality assurance, allowing them to verify that the pipes meet the specified requirements before installation. They also provide a baseline for future maintenance and monitoring, enabling engineers to track the performance of the pipes over time and address potential issues proactively.
The combination of 3PE coating, reinforced spiral steel, and comprehensive inspection reports makes these pipes ideal for a wide range of underground applications. In municipal water supply networks, they ensure the safe and reliable delivery of potable water, with the 3PE coating preventing contamination from soil chemicals and the spiral structure maintaining water pressure even in large-diameter mains. For natural gas distribution systems, the corrosion protection is vital to prevent leaks that could lead to explosions or environmental hazards, while the structural strength handles the high pressure of gas transmission. In sewage and wastewater networks, where the presence of corrosive gases and liquids is unavoidable, the 3PE coating resists degradation, reducing the need for frequent repairs and minimizing the risk of sewage leaks that pollute soil and groundwater. Industrial applications, such as chemical processing plants or power stations, also benefit from these pipes, as they can withstand the aggressive fluids and high temperatures often found in industrial waste systems.
Beyond their protective and structural benefits, 3PE anti-corrosion reinforced spiral steel pipes offer significant economic advantages over alternative materials. While the initial cost may be higher than uncoated steel or plastic pipes, their extended service life—often 50 years or more—results in lower lifecycle costs. Reduced maintenance, fewer replacements, and minimized downtime for repairs translate to substantial savings for municipalities and industrial operators. The 3PE coating also reduces the need for expensive corrosion mitigation measures, such as cathodic protection systems, in many applications. Additionally, the spiral manufacturing process allows for the production of large-diameter pipes, which are more cost-effective for high-volume fluid transport than multiple smaller pipes. For underground projects, where excavation and installation costs are significant, the durability of these pipes means that trenches need to be opened fewer times over the decades, reducing disruption to communities and lowering long-term construction costs.
Environmental sustainability is another key advantage of these pipes. By extending the service life of underground infrastructure, they reduce the demand for raw materials and energy required for manufacturing replacement pipes. The 3PE coating is inert and does not leach harmful substances into the soil or groundwater, ensuring compliance with environmental regulations and protecting ecosystems. In wastewater applications, their resistance to corrosion prevents leaks that could contaminate water sources, supporting efforts to preserve clean water supplies. The steel used in the pipes is also highly recyclable, contributing to a circular economy and reducing the environmental impact of construction waste.
In conclusion, 3PE anti-corrosion reinforced spiral steel pipes represent the pinnacle of protection and performance for underground pipe networks. Their multi-layered 3PE coating provides unrivaled resistance to corrosion, while the reinforced spiral steel structure ensures mechanical strength and durability. The attached inspection reports offer transparency and verification, giving stakeholders confidence in the pipes’ quality and reliability. Whether used in municipal water systems, gas pipelines, or industrial networks, these pipes deliver long-term performance, economic value, and environmental benefits that make them an indispensable choice for modern underground infrastructure. As cities expand and infrastructure ages, the demand for such advanced corrosion protection solutions will only grow, solidifying the role of 3PE anti-corrosion reinforced spiral steel pipes as a cornerstone of sustainable underground engineering.
More Products
Message
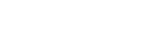
All Rights Reserved Copyright © RIZHAO STEEL HOLDING GROUP CO.,LTD. SEO 【Business license】
All Rights Reserved Copyright © RIZHAO STEEL HOLDING GROUP CO.,LTD.